Introduction
In today's manufacturing landscape, the ability to identify and address the root causes of issues is crucial for achieving operational excellence. Root Cause Analysis (RCA) software plays a vital role in this process, offering comprehensive analysis, actionable insights, and seamless integration to enhance operational efficiency. By leveraging the power of real-time data retrieval and quick implementation processes, organizations can minimize downtime and drive continuous improvement.
In this article, we will explore the importance of selecting the right RCA software and its impact on achieving operational excellence. We will discuss key features to look for in RCA software, such as comprehensive analysis capabilities, user-friendly interfaces, and advanced analytics. Additionally, we will examine case studies and real-world examples that highlight the value of rapid integration processes and cost considerations when choosing RCA software. By understanding these key factors, organizations can make informed decisions to optimize their operations and drive towards operational excellence.
1. Understanding the Importance of Root Cause Analysis in Manufacturing
Root Cause Analysis (RCA) holds a crucial position in the manufacturing domain. It presents a systematic approach that uncovers the principal causes of faults or issues. RCA's true worth is derived from its capacity to facilitate organizations in formulating and executing corrective measures that prevent the reoccurrence of these problems, thus enhancing operational efficiency.
In the manufacturing realm, downtime is a significant hurdle. It's not just an interruption in the production schedule, but also a gateway to financial losses. Here, RCA plays an indispensable role in the pursuit of downtime reduction. By pinpointing the root causes of problems and implementing corrective actions, RCA can substantially curtail downtime in manufacturing operations.
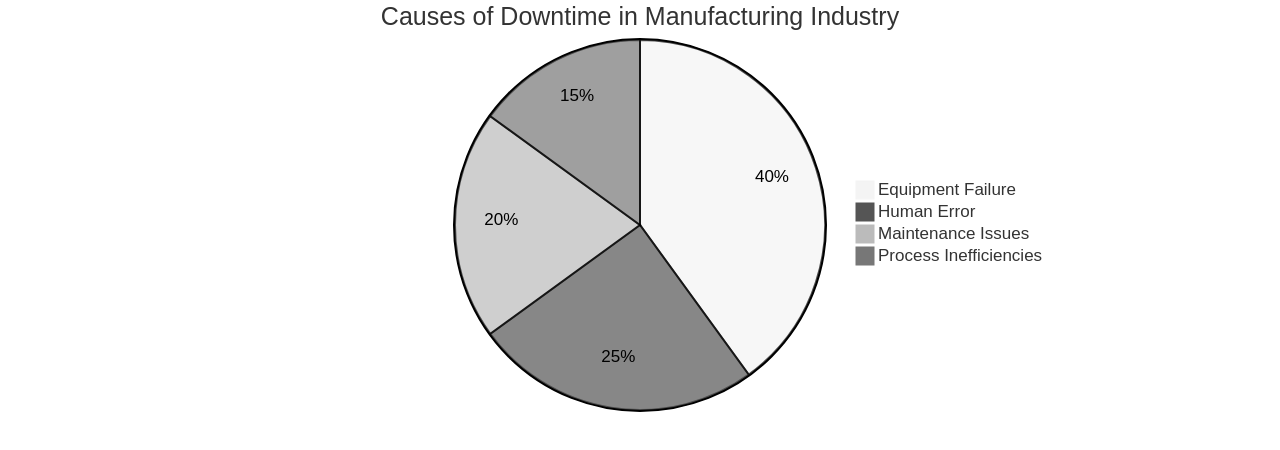
RCA's ultimate objective is to ensure the flawless operation of manufacturing processes. By identifying the root causes of issues and initiating corrective action, RCA assists in the continuous functioning of manufacturing operations. The result is a boost in the efficiency and effectiveness of the manufacturing industry, emphasizing RCA's importance.
To carry out effective RCA in manufacturing, it's crucial to adhere to a systematic approach. A widely adopted method is the '5 Whys' technique, which involves asking "why" repeatedly to unearth the root cause of a problem. The persistent questioning allows for a deeper analysis of the issue and discovery of the root cause. Furthermore, tools such as fault tree analysis and fishbone diagrams can be utilized to visually illustrate the causes and effects of a problem. These methods aid manufacturers in identifying the root cause of issues and implementing robust solutions to prevent recurrence.
For an effective RCA in the manufacturing sector, several best practices can be adopted:
By adhering to these best practices, manufacturers can bolster their ability to identify and address the root causes of problems, leading to more efficient and reliable manufacturing processes.
2. Key Features to Look for in Root Cause Analysis Software
Root Cause Analysis (RCA) software is a critical tool in the quest for operational efficiency and effectiveness. It's a solution that digs deep beyond the superficial issues to uncover the core reasons for operational inefficiencies, ensuring that comprehensive corrective measures are taken to prevent recurring issues.
A key feature to look out for in RCA software is its ability to provide a comprehensive analysis. This is achieved through advanced tools and algorithms that analyze various data points and patterns, helping to identify the root cause of a particular issue or problem. Moreover, the software should have the capability to integrate with other systems or databases to gather relevant data for a more thorough analysis.
The user interface of the software also plays a significant role in its effectiveness. It's important to choose software that offers intuitive navigation, clear visualizations, and easy-to-understand data representation. Interactive dashboards and customizable reports are also essential features that can aid in the analysis and identification of the root causes of issues.
One of the primary functions of RCA software is to provide actionable insights. These insights, drawn from data analysis and patterns, can help users identify the root causes and provide recommendations for improvement. This leads to more effective problem-solving and decision-making processes.
The software should also offer advanced analytics capabilities, including statistical analysis to help identify correlations and statistical significance between different variables. Furthermore, it should provide interactive visualizations, such as graphs and charts, to help users understand complex data and identify trends or anomalies.
Take the example of a company that conducted an RCA due to a high return rate of their baby strollers caused by a wheel falling off. They discovered that the wrong nut was used to tighten the wheels. After purchasing the correct nuts, they reduced the return rate. However, they later discovered that the axle onto which the nut is tightened also breaks off. By purchasing the axle component with strict specifications, they completely eliminated the return issue. This example illustrates how RCA software can help in identifying and resolving the root causes of problems, ultimately enhancing efficiency and customer satisfaction.
When choosing RCA software, it's important to consider factors such as data collection capabilities, collaboration features, integration with existing systems, automation, reporting and documentation, and scalability and flexibility. A software that checks all these boxes effectively addresses the root causes of problems and improves operational performance.
In the end, the right RCA software should not only help in identifying the root causes of problems but also guide the implementation of corrective measures. By leveraging RCA software, you can streamline the process of implementing corrective measures and ensure a more efficient and effective approach to problem-solving.
3. Evaluating the Integration Capabilities of RCA Software
The potential of Root Cause Analysis (RCA) software is underpinned by its ability to interlink with key systems within an organization. This interoperability, particularly with systems like Computerized Maintenance Management Systems (CMMS) and Enterprise Asset Management (EAM) systems, is a crucial facet of the software. The power of real-time data syncing across these platforms is key in executing accurate and prompt root cause analysis.
The universal compatibility of RCA software with a range of CMMS and EAM products bolsters its adaptability and efficacy. However, it is important to note that the RCA software's integration capability is not confined to specific platforms. For instance, the integration of RCA software with Oracle Fusion Cloud Warehouse Management can amplify businesses' operational efficiency by providing real-time insights into inventory, facilitating tracking and analysis of warehouse processes, and pinpointing the root causes of potential issues.
Furthermore, a seamless integration process between RCA software and SAP Extended Warehouse Management can be achieved by following the provider's guidelines, typically involving the configuration of necessary connectors or APIs. This exchange of data and information between the two systems enhances overall warehouse management capabilities.
Companies like Integral Group have demonstrated their expertise in creating API, EDI, apps, and integrations that cater to a wide range of industries, including retail suppliers, logistics providers, manufacturing suppliers, pharma companies, and software providers. Their work underscores the role of integration in boosting operational efficiency.
Examples such as the incorporation of the Zoho inventory module into a distributor's workflow and the outsourcing of EDI requirements for a warehousing and distributing provider, showcase the transformative potential of well-executed integrations. These instances exemplify how effective integration of RCA software with other systems can streamline processes, heighten operational efficiency, and contribute to reducing downtime in manufacturing.
In short, the integration capabilities of RCA software are fundamental to its effectiveness. The ability to integrate smoothly with various systems in the organization, sync data in real-time, and maintain compatibility with a variety of CMMS and EAM products, all contribute significantly to the software's utility in achieving operational excellence. Moreover, the benefits of real-time data syncing in root cause analysis are manifold. By analyzing the most current data, organizations can ensure accuracy and promptness in root cause analysis, identify and resolve issues faster, and enhance collaboration among stakeholders.
4. Case Study: How Makini Streamlines Data Syncing and Enhances Efficiency
In the sphere of industrial maintenance and asset management, the seamless integration and synchronization of data across various systems are paramount for operational efficiency. Let's take a look at two examples that illustrate this importance: Palmaz Vineyards and BookMyShow.
Palmaz Vineyards, a family-owned winery in Napa Valley, utilized a proprietary Machine Learning software, FILCS (Fermentation Intelligence Logic Control System), to gain valuable insights into the fermentation process. However, the substantial amount of data produced by FILCS presented a considerable challenge. The initial consideration of utilizing cloud services for storage was discarded due to limited scalability, access speed, and latency issues. They opted instead for an on-site solution, using Synology NAS devices for storage and running the FILCS software on virtual machines. This solution eliminated the bottlenecks associated with cloud computing and allowed FILCS to derive solutions promptly.
On the other hand, BookMyShow, a leading entertainment company in India, had a different challenge with its 15-year-old analytics solution. The legacy system, with multiple data copies and a variety of tools and technologies, led to inefficiencies and high costs. Their migration to a modern data architecture on AWS resulted in substantial cost savings - 90% in storage and 80% in analytics expenditure.
These examples underscore the importance of selecting the right technology for data integration and synchronization. In the case of Palmaz Vineyards, Synology's solutions provided speed, scalability, and affordability for effective wine-making data analysis. For BookMyShow, AWS's modern data architecture offered scalability, agility, cost savings, and improved data sharing and governance.
However, in an industrial maintenance context, integrating a solution like Makini with Computerized Maintenance Management Systems (CMMS) can also be an effective strategy. This integration process involves identifying your CMMS system, checking its support for API integration, navigating to Makini's "Integrations" section, and following the instructions provided by Makini to set up the integration. The integration enables seamless data transfer between Makini and your CMMS system.
Makini also offers various integrations, such as Oracle Fusion Cloud Warehouse Management and Snapfulfil, allowing for data syncing between different systems. You can find examples of data syncing using the Makini API on their website.
When integrating Makini with a CMMS, it is important to follow best practices. These include ensuring that the CMMS is compatible with Makini, using a standardized data exchange format such as JSON or XML, establishing a clear data mapping and synchronization process, considering the frequency and timing of data synchronization, and performing thorough testing and validation of the integration.
In conclusion, whether you're a winery in California or an entertainment company in India, the right integration strategy can greatly enhance efficiency, streamline data syncing processes, and ultimately, contribute to the bottom line.
5. The Role of Real-Time Data Retrieval in Effective RCA
Real-time data access has a pivotal role in the process of root cause analysis (RCA), offering organizations the ability to quickly pinpoint and scrutinize possible issues. This swift identification allows for the implementation of corrective actions, thereby reducing operational downtime.
A striking illustration of this is the Central Group, a major retail conglomerate in Asia. Through the use of a real-time analytics data engine known as QuestDB, they can consolidate data from diverse online and offline sources, creating actionable dashboards for each business unit's specific teams. This instant data visualization is critical for monitoring and promptly addressing any unusual data patterns.
However, the adoption of Makini's API could further enhance this approach. Makini provides real-time data retrieval from an array of sources, bringing up-to-date information from preferred data sources to the fingertips of decision-makers. The Central Group could harness the power of Makini to further streamline their data aggregation and visualization processes, leading to even more efficient monitoring and response to data anomalies.
The transformation of the Central Group's marketing performance tracking through the use of QuestDB is another testament to the power of real-time data. Dynamic comparisons between various advertisement platforms across selected time spans became possible, thanks to the real-time data provided by QuestDB. This allowed the company to correlate online sales with the physical presence of their department stores, delivering insights into their offline business performance. The integration of Makini's API could further enhance these capabilities, providing a more comprehensive view of real-time data across various marketing channels.
The Royal Bank of Canada's (RBC) implementation of the Confluent Platform for real-time data streaming is another clear demonstration of the transformative potential of real-time data retrieval. The switch to an event-based architecture and the initiation of a microservices transformation led to improved customer service quality, faster and scalable applications, and a reduction in anomaly detection time from weeks to seconds. The potential for the integration of Makini's API in such a setting is noteworthy, offering further enhancements in data streaming, improving anomaly detection times, and facilitating data reuse across teams for more pertinent business insights.
The Central Group and RBC's experiences underscore the transformative potential of real-time data retrieval for RCA. By incorporating real-time data retrieval tools such as QuestDB, Confluent, and Makini's API into their operations, organizations can swiftly identify and tackle issues. This rapid response significantly reduces downtime and boosts overall operational efficiency.
6. How Rapid Integration Processes Contribute to Downtime Reduction
Rapid integration processes play a significant role in minimizing operational downtime. The pace of these processes is directly linked to data synchronization speed, which in turn allows for quick identification and resolution of issues. Companies such as Makini, Bayer Crop Science, and Heineken have demonstrated the potential of swift integration.
Makini, popular for its industrial integrations, is known to develop these within a week or two. This promptness helps in significantly reducing downtime and enhancing operational efficiency. Rapid integration in industrial maintenance and asset management systems, as demonstrated by Makini, offers several benefits. It allows for seamless connectivity between different systems, enabling real-time data sharing and communication. This can lead to improved efficiency and productivity in maintenance operations, as it enables quick access to relevant information and facilitates faster decision-making.
Similarly, Bayer Crop Science revamped their integration strategy with MuleSoft's Anypoint Platform to overcome hurdles in product development. This shift towards API-led connectivity offered a unified view of customer data, improved customer service, and reduced maintenance and support costs. The outcome was a 200% increase in product development speed, a fivefold increase in time to market, and a 70% decrease in process functions. One way to reduce downtime with fast integration processes in industrial systems, as exhibited by Bayer, is by using efficient and reliable integration solutions. These solutions can streamline the integration process, ensuring that data and systems are seamlessly connected and synchronized.
Heineken's Evergreen Initiative aspired to become the world's "best connected brewer". To achieve this, Heineken collaborated with IBM Consulting to create integration capabilities that connected its global network of brewers, customers, and business partners. The integration platforms handled business-critical applications, automation, and messaging at scale. To improve operational efficiency through fast integration processes, it is important to streamline the integration of various systems and platforms. By integrating systems such as Oracle Fusion Cloud Warehouse Management and SAP Extended Warehouse Management, organizations can enhance their operational efficiency by automating processes, reducing manual tasks, and improving data accuracy.
Therefore, the importance of rapid integration processes in downtime reduction cannot be overstated. Their success stories serve as a beacon for other companies to follow, highlighting the tangible benefits of rapid integration in the manufacturing industry. By integrating systems such as warehouse management systems (WMS), enterprise resource planning (ERP) systems, and customer relationship management (CRM) tools, companies can achieve real-time visibility, optimize inventory management, and enhance overall productivity.
7. Cost Considerations when Choosing an RCA Software: The Value of No Extra Charges
Considering the critical role of cost in the decision-making process for Root Cause Analysis (RCA) software, it is paramount to find a solution that delivers robust features without straining your budget. In this context, several cost-effective RCA software options are gaining popularity in the market, offering a remarkable value proposition.
For instance, TapRooT is known for its user-friendly interface and systematic approach to identifying and rectifying root causes of problems. It provides a detailed process for conducting investigations and generating reports, ensuring a comprehensive understanding of the issues at hand.
Similarly, Apollo RCA, a cloud-based solution, enables teams to conduct investigations remotely. It offers features like cause and effect mapping, action tracking, and trend analysis. These features allow for efficient collaboration and in-depth analysis, enhancing the process of problem-solving.
In the same vein, RCA Software offers a comprehensive solution with tools for identifying and analyzing root causes. It also allows for the implementation of corrective actions and tracks their effectiveness, ensuring that the issues are not only identified but also effectively resolved. This software also boasts customizable workflows and reporting capabilities, allowing for a personalized approach to RCA.
Another noteworthy player in the market is Sologic. It offers a range of features, including cause and effect analysis, evidence gathering, and action tracking. In addition, Sologic also provides training and certification programs for RCA practitioners, ensuring that users are well-equipped to leverage the software effectively.
Lastly, Incident Analyzer, an RCA software, focuses on analyzing incident data to identify patterns and trends. It provides a visual interface for exploring data and generating insights, making the process of RCA more intuitive and insightful.
While considering these cost-effective RCA software options, it is important to note that there is no specific mention of free integration services for these software options. Therefore, while they deliver value in terms of affordability and features, additional expenses might be incurred for advanced integration capabilities.
In the market, other players also offer value propositions. For instance, Flexera One provides a comprehensive view of different business services, from business service mapping to integration with other systems. It also provides asset management solutions and focuses on cloud migration planning and cost optimization. This holistic approach enables organizations to optimize their technology investments.
Flexera One's latest collaborations, awards, and product enhancements further underscore its commitment to delivering value to its customers. For example, its collaboration with IBM to bring asset management to new Z16 LinuxOne 4 single frame rack mount models showcases its innovative approach. Flexera's FinOps Think Tank and the 2023 State of Cloud Report provide valuable insights into cloud computing trends and statistics.
Additionally, Audinate offers insights into AV networking through its newsletter, Networds. This bi-monthly publication covers a wide array of topics, including audio, video, networking, AV over IP, and more. It also provides information about Dante, a networking technology for audio and video over IP.
In conclusion, as an Operations Director, the goal is to select an RCA software that aligns with your organization's strategic objectives and fits within your budget. Whether it's the cost-effectiveness of the aforementioned solutions or Flexera One's comprehensive offerings, the key is to choose a solution that delivers maximum value for your investment.
8. Achieving Operational Excellence with the Right RCA Software
The integration of a robust Root Cause Analysis (RCA) software is a key step towards achieving operational excellence. An effective RCA software is characterized by comprehensive analysis, user-oriented interface, actionable insights, advanced analytics, seamless integration, real-time data retrieval, and quick implementation processes. These features can significantly enhance operational efficiency by reducing downtime and enabling prompt resolution of issues, thus aiding organizations in effectively achieving their strategic goals.
In the manufacturing sector, the significance of rapid and seamless integration is demonstrated by the experiences of Baoti Group and Boeing. Baoti Group, a major producer of titanium and titanium alloys and a key supplier to Boeing, selected the CData ARC platform for implementing electronic data interchange (EDI) integration with Boeing, a globally recognized aviation manufacturer. The CData ARC platform, which enables secure communication with hundreds of applications, databases, and services, allows Baoti Group to efficiently exchange EDI X12 purchase orders and messages, hence ensuring seamless interaction with Boeing's EDI system. This integration has led to efficient order processing, smooth communication, enhanced visibility of demand forecasts, and improved operational efficiency.
Likewise, British Airways (BA) needed to upgrade their data center infrastructure management (DCIM) tools. They needed a solution that could speed up server allocation, provide instant reporting, and real-time dashboards of power and cooling capacity. They found their solution in Raritan's DCIM software, DCTrack, which offered an easy-to-use and flexible platform. Consequently, BA can now manage server power and network connectivity, allocate space for new servers, issue work orders, and provide capacity planning across all its data centers.
These instances highlight the importance of seamless integration and real-time data retrieval in RCA software. A company such as Makini.io offers integration solutions for various software applications, including RCA software. By utilizing these solutions, organizations can streamline their RCA processes, thus enhancing the efficiency of their software systems.
In order to achieve real-time data retrieval in RCA software, techniques such as using the fetch() function in JavaScript can be utilized to make an HTTP request to an API endpoint that provides the necessary data. By specifying the API URL and the necessary request options, such as the method and headers, the response can be extracted and used for further analysis or display.
When selecting the right RCA software for operational efficiency, it's crucial to evaluate its ability to analyze and identify the root causes of issues accurately and efficiently. Look for features such as advanced data analytics, visualization tools, and automated root cause identification. Consider the software's integration capabilities, ensuring it can seamlessly integrate with existing systems and data sources. The software's user interface should be user-friendly, allowing for easy navigation and quick access to relevant information. Features such as customizable dashboards, real-time alerts, and interactive reporting are beneficial. In addition, consider the software's scalability and flexibility, ensuring it can grow with your organization and adapt to changing business needs. Lastly, consider the software's vendor support and reputation, looking for a reliable vendor that provides ongoing support, regular updates, and has a solid reputation in the industry.
By considering these factors, organizations can select the right RCA software that will improve operational efficiency and effectively identify and resolve root causes of issues, ultimately leading to the successful achievement of their strategic goals and objectives.
Conclusion
The main points discussed in this article highlight the importance of selecting the right Root Cause Analysis (RCA) software for achieving operational excellence in manufacturing. RCA plays a crucial role in identifying and addressing the root causes of issues, leading to enhanced operational efficiency. The ability to minimize downtime through comprehensive analysis, user-friendly interfaces, and advanced analytics is essential for optimizing manufacturing processes. Real-world examples demonstrate how rapid integration processes and cost considerations contribute to reducing downtime and improving overall efficiency. By understanding these key factors and implementing effective RCA software, organizations can streamline their operations and drive towards operational excellence.
In conclusion, selecting the right RCA software is essential for achieving operational excellence in the manufacturing industry. Comprehensive analysis capabilities, user-friendly interfaces, and advanced analytics are key features to look for when choosing RCA software. Rapid integration processes and cost considerations also play a significant role in minimizing downtime and optimizing efficiency. By leveraging the power of real-time data retrieval and quick implementation processes offered by RCA software, organizations can address root causes effectively, minimize downtime, and drive continuous improvement. To optimize operations and achieve operational excellence, organizations should start now by selecting the right RCA software that meets their specific needs.