Introduction
Optimizing efficiency and improving operational performance are top priorities for manufacturing organizations. One key strategy that plays a crucial role in achieving these goals is preventive maintenance. By regularly inspecting and maintaining equipment, organizations can prevent unexpected failures, reduce downtime, and extend the lifespan of their assets. In this article, we will explore the importance of preventive maintenance in manufacturing and the role of integrated systems in streamlining operations. We will also discuss the benefits of leveraging data analytics and automation to enhance preventive maintenance strategies. By implementing these practices, organizations can improve operational efficiency, reduce costs, and ensure a safe and productive work environment.
1. Understanding the Importance of Preventive Maintenance in Manufacturing
Preventive maintenance is a key strategy in manufacturing that involves regular equipment inspections and upkeep to prevent unexpected failures. By identifying potential issues early on, this proactive approach helps to reduce unplanned downtime and improve overall equipment efficiency. Moreover, it extends the equipment lifespan and diminishes the need for expensive repairs or replacements, thus preserving financial resources.
The use of Minitab statistical software is a significant asset in creating preventive solutions. It helps organizations in analyzing data and designing preventative maintenance strategies. Understanding the power of data, manufacturers can achieve significantly lower costs in product development and operation.
In addition to reducing costs, preventive maintenance enhances workplace safety by ensuring that equipment is functioning properly, thereby reducing the risk of accidents. The China Manufacturing Consultants (CMC) stresses the importance of preventive maintenance in manufacturing operations, as high-tech equipment presents more failure modes. The transition from reactive to preventive maintenance involves understanding the impact of poor maintenance, planning preventive actions, implementing total productive maintenance (TPM), and working with data through reliability-centered maintenance (RCM).
Implementing preventive maintenance involves a systematic approach, including regular equipment inspections, creating a preventive maintenance schedule, conducting routine maintenance tasks, and utilizing condition-based monitoring.

The use of a computerized maintenance management system (CMMS) can be particularly beneficial in managing these processes.
Further, it is crucial to develop a comprehensive preventive maintenance plan. This involves creating an inventory of all equipment used, analyzing each item to determine its criticality and failure modes, identifying the necessary maintenance tasks for each item, determining the frequency of these tasks, documenting and tracking all maintenance activities, providing necessary training and resources to the maintenance team, and continuously reviewing and evaluating the plan for improvement.
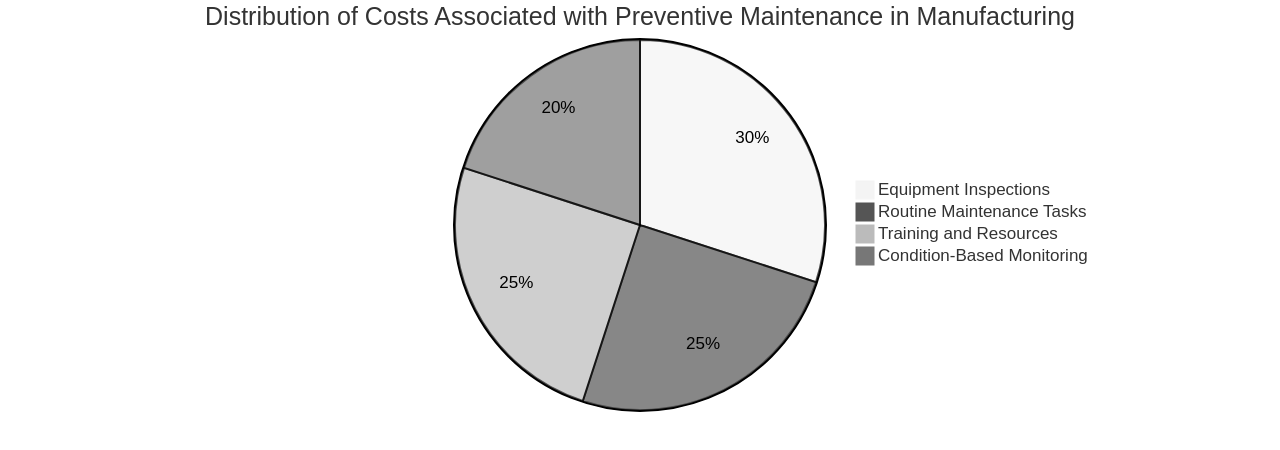
In the end, preventive maintenance is a crucial aspect of successful manufacturing operations, significantly contributing to cost reduction, equipment longevity, and prevention of system failures.
2. Identifying Potential Challenges and Solutions in Implementing Preventive Maintenance Strategies
Preventative maintenance strategies are often obstructed by gaps in skilled workforce, data scarcity, and resistance to change. However, these barriers can be overcome by investing in skill enhancement programs, leveraging technology for data collection and interpretation, and fostering a culture that embraces ongoing improvement.
Several software solutions have been developed by companies such as Minitab to enable proactive preventative maintenance strategies. These software tools utilize data analytics techniques to predict and prevent potential failures. For instance, predictive maintenance software and health monitoring systems have been successfully integrated into operations by companies like Baker Hughes and Mondi, demonstrating the power of data-driven preventive maintenance strategies.
In addition, platforms such as Makini provide a universal API for industrial maintenance and asset management systems, enhancing data management efficiency and accessibility. The McKinsey Global Institute found that manufacturing companies can lower costs in product development and operating costs by up to 50 percent and 25 percent respectively by harnessing the potential of their data.
To address resistance to change, it's crucial to communicate the benefits of preventive maintenance strategies. This includes how they can reduce downtime, extend equipment lifespan, and increase overall operational efficiency.
Involving employees in decision-making processes and providing them with adequate training and support can also help build buy-in for change.
Implementing a universal API for industrial maintenance brings about several benefits. It enables smoother integration between different systems and software used in industrial maintenance, leading to improved efficiency and productivity. Furthermore, a universal API facilitates better data analytics and reporting by integrating various maintenance systems through a common API, leading to more effective and consistent maintenance practices across the organization.
In terms of data analysis in preventive maintenance, best practices include collecting and analyzing historical maintenance data to identify patterns and trends. This helps in predicting equipment failures and scheduling maintenance activities accordingly. Leveraging data analysis can significantly improve the effectiveness of preventive maintenance strategies.
To foster a culture of continuous improvement in maintenance, organizations can implement strategies such as encouraging open communication and collaboration among team members. This can be done through regular team meetings where employees can share their ideas, experiences, and suggestions for improving maintenance processes. Creating a supportive and positive work environment, where employees feel empowered to contribute their ideas and take ownership of their work, is also crucial in fostering a culture of continuous improvement in maintenance.
In summary, implementing preventive maintenance strategies can indeed be challenging, but these challenges can be surmounted with the right tools, training, and a culture of continuous improvement.
3. The Role of Industrial Integration in Preventive Maintenance
Industrial integration serves as a cornerstone in preventive maintenance, enabling seamless data communication among various systems. This enables real-time equipment monitoring, predictive analytics, and automated maintenance task scheduling. It's akin to having a sixth sense for the health of your machinery and knowing when it might need attention.
Platforms such as Makini can accelerate such integrations, allowing companies to promptly and effectively execute preventive maintenance strategies. This is crucial in the modern manufacturing landscape where downtime can be expensive. The data generated from these integrations can offer a wealth of insights. For example, historical operating data can be used to predict future equipment failures, allowing for proactive maintenance. This shift from reactive to predictive maintenance can help overcome the challenges associated with implementing true predictive maintenance systems.
Moreover, the merging of IT and OT (Operational Technology) is transforming industrial operations. Technological advancements like IoT, big data analytics, and machine-to-machine communication are driving this convergence, leading to enhanced manufacturing production and reliability.
Furthermore, efficient management of plant assets is essential for competitiveness, cost management, and production optimization. By addressing abnormal conditions and process disturbances quickly, incidents and economic loss can be prevented.
In essence, industrial integration is not merely about connecting systems. It's about harnessing the power of data to predict, prevent, and optimize. It's about revolutionizing the way we approach preventive maintenance, making it a strategic tool for operational excellence.
To implement industrial integration for preventive maintenance, there are several steps to follow. First, identify the systems and equipment that need integration. Choose a suitable integration platform or software that can connect these systems and equipment. Configure the platform to collect data from various systems and equipment. Implement predictive analytics algorithms or machine learning models to analyze the collected data and identify patterns or anomalies that could indicate potential maintenance issues. Set up automated alerts or notifications to inform maintenance personnel about the identified issues.

Develop a preventive maintenance schedule based on the insights provided by the integration platform. Monitor the performance of the integrated systems and equipment on a regular basis.
With Makini, you can achieve real-time monitoring and predictive analytics in industrial maintenance. Makini provides a comprehensive platform that allows you to monitor and analyze industrial maintenance processes in real-time. By integrating with Makini's platform, you can gather data from various sources and utilize predictive analytics algorithms to identify potential issues before they occur.
In conclusion, remember that it's not just about connecting systems. It's about leveraging the power of data to predict, prevent, and optimize. It's about transforming the way we approach preventive maintenance, making it a strategic tool for operational excellence.
4. Streamlining Operations through Effective Integration of CMMS and EAM Products
Integrating Computerized Maintenance Management Systems (CMMS) with Enterprise Asset Management (EAM) tools can significantly enhance operational efficiency. This combination creates a unified platform for managing all maintenance activities, tracking assets, and analyzing data.
For instance, Pentalon Construction, a multi-family and commercial construction management firm, adopted CMIC, a fully integrated software, as their projects grew in complexity. CMIC brought improved system communication and ensured data transfer reliability. It provided features that simplified project management operations like managing and automating notifications of RFIs and submittals. It also improved accounting processes, particularly in efficiently processing change orders.
CMIC Field, a part of the CMIC platform, provided project managers with visibility into all project management operations. It also offered forecasting capabilities and easy access to project data, which facilitated swift issue resolution and potential delay tracking. Around 50 employees at Pentalon use CMIC, and they plan to onboard marketing and management team members soon. The integration of CMIC not only led to cost savings but also provided a unified system that significantly improved their operations.
Likewise, Makini's universal API presents a consolidated view of all maintenance and asset management activities by integrating various CMMS and EAM products. This integrated approach to asset management and maintenance is not just a trend but a proven strategy for operational efficiency, as demonstrated by Pentalon Construction.
5. Utilizing Universal API for Efficient Data Management and Real-Time Data Retrieval
Integrating universal APIs into your data management systems can significantly streamline your operations. The use of APIs such as Makini's can unify data structures, authorization protocols, and data transformations, simplifying the overall data management process. This can lead to more efficient decision-making and proactive maintenance scheduling, enhancing operational efficiency.
For example, real-time data updates can be displayed in applications using MongoDB change streams. Coupled with the Realm Web SDK, a real-time data display can be created in a React JavaScript front-end. This involves the use of an Atlas cluster, specifically the free tier, and the creation of a new database named "data" with a collection called "changestream". The application listens for changes in the "changestream" collection and displays these changes in a table in real-time.
Furthermore, the integration of generative AI solutions, such as PubNub with OpenAI's GPT, can improve real-time communication and messaging experiences. PubNub offers a platform with features like solution kits, PubNub Insights, edge messaging, network security, compliance, and integrations. This enables functionalities like chat, live audience engagement, multi-user collaboration, device control, data streaming, geolocation, dispatch, edge message bus, and enterprise SaaS.
However, implementing universal APIs for data management requires careful planning and execution. It involves identifying the API, obtaining API documentation, authenticating with the API, building API requests, implementing API calls, handling API responses, and monitoring and maintaining the API integration.
Best practices include defining a clear data model, using industry-standard protocols, implementing secure authentication, documenting and versioning the API, and monitoring API usage and performance. By adhering to these practices, organizations can effectively implement a universal API for data management, enabling seamless integration and efficient data exchange between different systems and applications.
In the grand scheme of things, the use of universal APIs, real-time data updates, and AI integrations can greatly improve data management and real-time data retrieval, leading to improved operational efficiency.
6. Optimizing Inventory Management through Integrated Systems
Inventory management is a pivotal part of manufacturing organizations, and the fusion of modern systems can greatly enhance its efficacy. For instance, Makini.io, an innovative inventory management solution, offers both on-premise and cloud-based functionalities. This platform provides real-time inventory surveillance across all locations, automates essential business functions, and provides robust order fulfillment capabilities.
Key features of Makini.io include automatic purchasing, which aids in reconciling accounting and calculating true landed costs automatically. It also provides vendor management capabilities, allowing businesses to manage costs, lead times, and part numbers across various vendors. The platform can integrate with other business functions, effectively streamlining the inventory management process.
The effectiveness of Makini.io is demonstrated in the case of KidWind, an educational initiative that faced challenges in inventory tracking and defining job roles. Prior to implementing Makini.io, KidWind relied on handwritten notes for inventory tracking, leading to disorder and inaccuracies. After deploying Makini.io, KidWind was able to define employees' roles, automate inventory management, and reduce on-hand inventory costs significantly.
In the same vein, the Mississippi State Department of Health (MSDH) utilized Makini.io's capabilities to enhance their emergency warehouse operations. During the H1N1 influenza outbreak, the Makini.io system enabled MSDH to deploy pandemic influenza assets to various facilities in an efficient and timely manner. As a result, MSDH is recognized as a national leader in handling strategic national stockpile assets.
The integration of modern systems like Makini.io can notably improve inventory management processes. It provides real-time visibility into inventory levels, automates reordering processes, reduces inventory carrying costs, prevents stockouts and overstocks, and enhances customer satisfaction.
7. Enhancing Aftermarket Processes for Improved Operational Performance
Enhancing the efficiency of aftermarket operations, particularly in areas such as equipment upgrades and parts replacement, can be significantly boosted through the application of integrated systems. These systems, such as Oracle Fusion Cloud Warehouse Management and JD Edwards Enterprise One, provide real-time visibility into inventory and orders, automating workflows, and enabling effective collaboration between departments.
The integration of these systems not only boosts operational performance but also elevates the quality of customer service. By ensuring maintenance and upgrades are executed promptly, customer experience is significantly enhanced.
An example of this is Ascend Performance Materials, a company that has integrated Seeq into their workflow. This integration facilitated data-driven decision-making and increased process capability at Ascend, showcasing the potential benefits of integrating such systems into aftermarket processes.
Moreover, a comprehensive and well-implemented integrated system, such as those provided by Makini.io, can lead to a substantial reduction in non-value-added activities, greatly improving the overall customer experience. The ultimate objective should be to employ these systems to create a lean, efficient, and customer-focused aftermarket process that propels operational performance to new heights.
By utilizing the integrations offered by platforms like Makini.io, organizations can obtain real-time data on equipment performance during aftermarket processes. This data can then be used to analyze and optimize your aftermarket operations. Predictive maintenance approaches can also be employed, using data analysis techniques to monitor equipment condition and predict when maintenance should be performed.
To automate the ordering process for aftermarket upgrades, integrations with systems like Oracle Fusion Cloud Warehouse Management or JD Edwards Enterprise One can be leveraged. These integrations can assist in automating tasks such as generating purchase orders, tracking inventory, and managing deliveries, ultimately improving the overall aftermarket upgrade ordering process.
8. Leveraging Rapid Industrial Integrations to Reduce Downtime
Rapid industrial integrations have proven to be a game-changer in reducing downtime and improving operational efficiency. This is evident from the success stories of companies like Bayer Crop Science and Swire Coca Cola, who have harnessed the power of API-led integrations and cloud migrations to achieve remarkable results in their operations.
The key to their success lies in the integration of various systems, such as Oracle Fusion Cloud Warehouse Management and SAP Extended Warehouse Management, to streamline and automate maintenance processes. Such integrations have enabled real-time data exchange between different systems, allowing for better monitoring of equipment and early detection of potential issues. This, coupled with predictive maintenance strategies that leverage data analytics and machine learning algorithms, has allowed for the identification of patterns and prediction of equipment failures.
Take, for instance, the benefits of integrating with warehouse management systems such as Oracle Fusion Cloud Warehouse Management and Manhattan Associates Warehouse Management IBM. These integrations streamline processes, optimize inventory management, and enhance overall operational effectiveness, leading to faster and more efficient workflows, and ultimately, improved productivity and cost savings.
Moreover, platforms like Makini.io offer a range of integrations that can be leveraged to automate the scheduling of maintenance tasks in an industrial setting. This ensures that maintenance tasks are scheduled and executed efficiently, reducing the risk of equipment failure and downtime.
These real-world examples serve as a testament to the power of rapid industrial integrations in minimizing downtime and enhancing operational efficiency. By employing similar strategies, organizations can leverage the benefits of real-time data retrieval, predictive analytics, and automated maintenance scheduling to minimize equipment failures and unplanned downtime. The result is an increase in operational efficiency and productivity, setting the stage for a more resilient and agile business model.
Conclusion
In conclusion, preventive maintenance plays a crucial role in manufacturing organizations by optimizing efficiency and improving operational performance. By regularly inspecting and maintaining equipment, organizations can prevent unexpected failures, reduce downtime, and extend the lifespan of their assets. The use of integrated systems, such as Makini's universal API, streamlines operations by enabling seamless data communication among various systems. Leveraging data analytics and automation further enhances preventive maintenance strategies, leading to improved operational efficiency, reduced costs, and a safe work environment.
The broader significance of these ideas is that implementing preventive maintenance practices can have a significant impact on manufacturing operations. By adopting a proactive approach to equipment maintenance, organizations can reduce costs associated with unplanned downtime and expensive repairs or replacements. Preventive maintenance also contributes to workplace safety by ensuring that equipment is functioning properly. Integrated systems and data analytics provide valuable insights for predictive maintenance, allowing organizations to identify potential issues before they occur. By embracing these practices and leveraging technology like Makini's universal API, organizations can optimize their operations for maximum efficiency.