Introduction
The implementation of the Six Sigma methodology in manufacturing is a powerful approach to eliminating defects and optimizing operational efficiency. By utilizing statistical tools and techniques, businesses can identify process inefficiencies, analyze data, and implement improvements to enhance product quality and customer satisfaction. Industrial integration platforms like Makini play a crucial role in streamlining data transmission, enabling real-time monitoring, and facilitating informed decision-making.
In this article, we will explore the impact of implementing Six Sigma on strategic goals and objectives in manufacturing. We will examine real-world case studies that demonstrate the effectiveness of Six Sigma in improving operational efficiency, reducing costs, and enhancing customer satisfaction. Additionally, we will discuss the role of industrial integration platforms like Makini in enabling seamless data synchronization and promoting collaboration across departments. By understanding the benefits of Six Sigma and effective industrial integration, businesses can achieve their strategic objectives and drive success in the manufacturing industry.
1. Understanding the Six Sigma Methodology in Manufacturing
Six Sigma, a data-driven methodology, is designed to eliminate defects and minimize variability in manufacturing and business processes. It utilizes statistical tools and techniques to identify process inefficiencies, evaluate performance, analyze data, and implement improvements. The goal is to enhance product quality and operational efficiency, leading to increased customer satisfaction and cost savings. Six Sigma projects in manufacturing often involve reducing waste, improving cycle times, and enhancing product quality.
Six Sigma is beneficial across a wide range of industries, including but not limited to government, healthcare, finance, education, agriculture, automotive, aviation, consumer products, energy, natural resources, hospitality, construction, machinery equipment, media entertainment, oil and gas, professional services, retail, technology, and telecommunications.
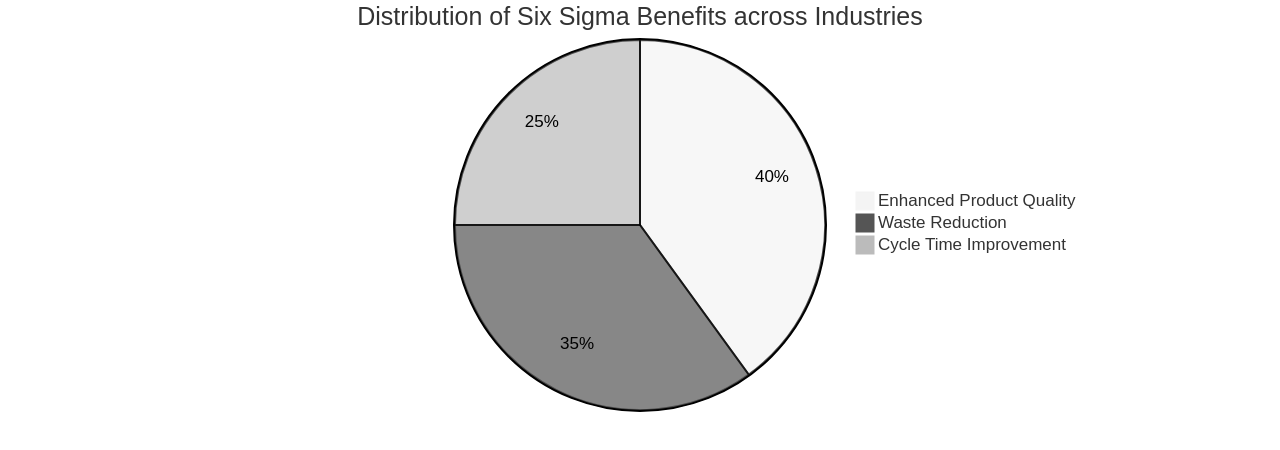
There are online platforms that offer comprehensive learning paths for Lean Six Sigma, including Yellow Belt, Green Belt, Black Belt, and Master Black Belt. These platforms include a learning management system, allowing users to access extensive online learning materials. Data-driven reporting tools deliver valuable insights, promoting organizational growth.
One notable example of Six Sigma in action is a food processing equipment manufacturer that saved $240,000 in annual warranty claims by implementing Lean Six Sigma principles. The manufacturer identified a gap in process performance and the 60-day deadline for warranty claims, initiating a Lean Six Sigma project. The manufacturer conducted a process gemba walk to identify waste and areas for improvement in the warranty claims process. Targeted solutions were implemented, such as defining roles and responsibilities, creating standard work and visual management, and providing training.
The improvements resulted in a significant reduction in cycle time, improved claim validity determination, and cost savings for the manufacturer. The manufacturer intends to apply the learnings from this project to future projects to further enhance organizational performance.
Another instance where Lean Six Sigma methodologies were beneficial was in the Kern County Probation Department, where they saved $400,000 in labor hours. The Tennessee Valley Authority also utilized Lean Six Sigma to close a budget gap of $21 million. These real-world examples and case studies highlight the effectiveness of Lean Six Sigma tools across different industries.
With its comprehensive approach and proven success across various industries, Six Sigma is a vital tool in the pursuit of operational excellence and improved customer satisfaction in manufacturing.
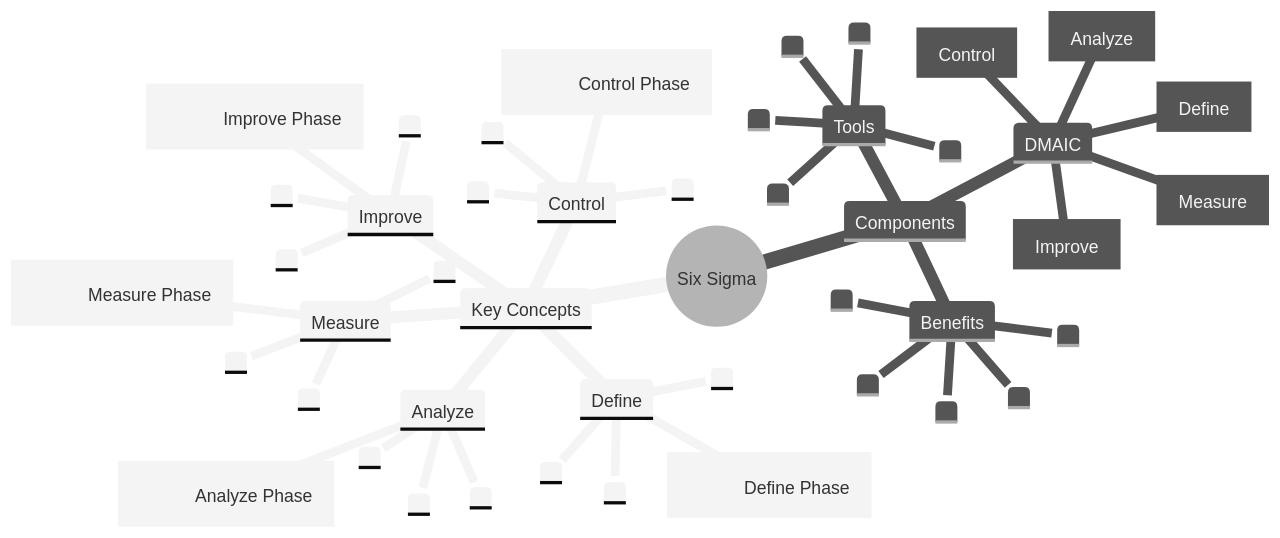
To find more case studies related to successful Six Sigma projects in manufacturing, one can visit makini.io and use the search or navigation features on the website.
2. The Role of Industrial Integration in Six Sigma Implementation
Industrial integration forms a vital nexus in the successful application of Six Sigma within the manufacturing landscape. It serves as a conduit for seamless data transmission across various systems, enabling real-time monitoring and analysis of operational data.
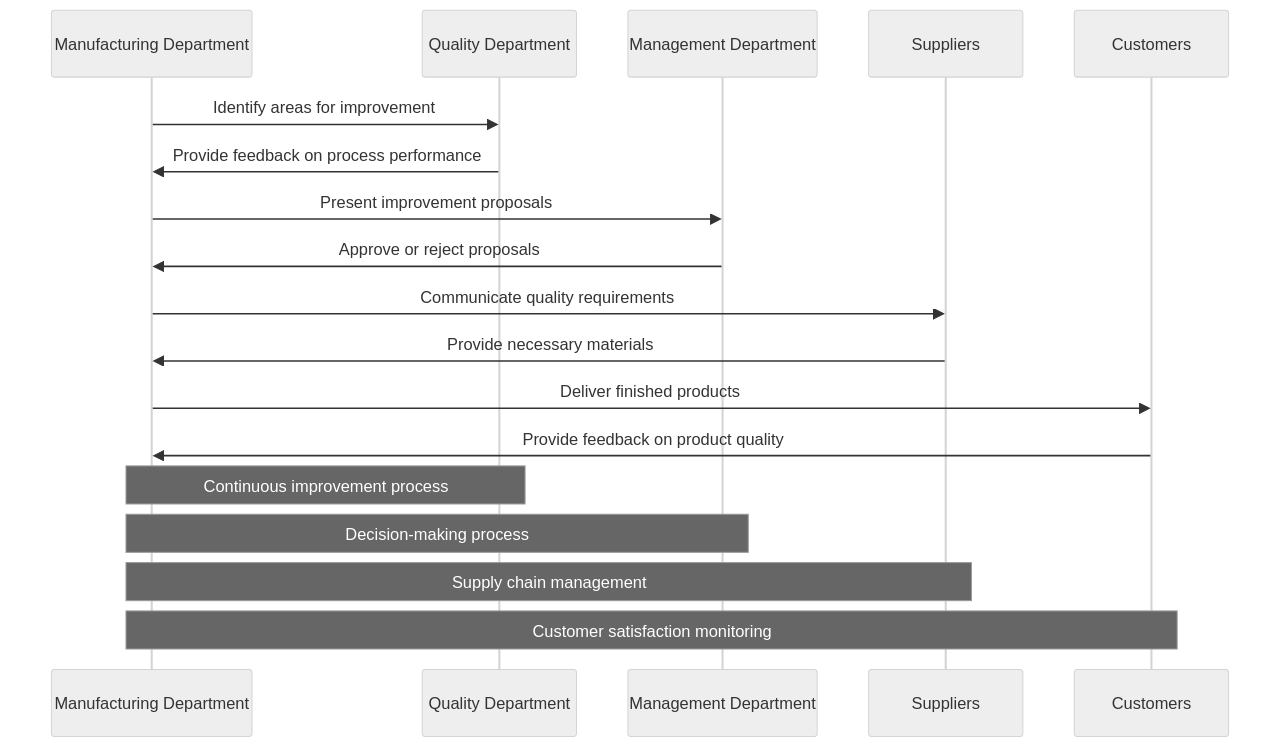
In this regard, tools like Makini play an indispensable role. Makini's universal API acts as a mediator, allowing for effortless data synchronization across different CMMS or EAM systems. This eradicates the need for managing multiple data structures and authentication protocols, thereby simplifying the integration process.
This streamlined integration is pivotal for the data-driven decision-making process at the heart of the Six Sigma methodology. This characteristic has rendered Makini a precious asset in the manufacturing sector. The roots of Six Sigma trace back to Motorola in 1981 when the company was endeavoring to contest with Japanese firms boasting superior quality measures. Against all odds, Motorola achieved a tenfold improvement in quality across all business divisions within five years, effectively laying the groundwork for Six Sigma's ascendance.
Motorola's real-world success story of Six Sigma application highlights the transformative potential of this methodology in boosting competitiveness. This success inspired other companies to adopt Six Sigma in their pursuit of comparable benefits. This methodology, far from being a mere statistical measure, serves as a strategic tool for organizations, offering operational benefits like enhanced efficiency and cost reduction.
The use of Six Sigma extends beyond the manufacturing sector. Consider Kyocera Corporation, which has diversified its business into communications, automotive, environmental energy, and healthcare. In pursuit of its ambitious target of increasing sales from JPY 16 trillion to JPY 2 trillion, Kyocera has initiated a 'productivity doubling project'. This project revolves around autonomous production, where AI analyzes real-time data and adjusts to prevent defects and machine malfunctions. This initiative has already resulted in improvements in yield rate and defect reduction.
In sum, be it a manufacturing behemoth like Motorola or a diversified corporation like Kyocera, the implementation of Six Sigma, enabled by industrial integration platforms such as Makini, has emerged as a revolution in enhancing operational efficiency and competitiveness. While Makini's integration capabilities with Six Sigma or other manufacturing systems aren't explicitly mentioned, it does offer integrations with various systems like Oracle Fusion Cloud Warehouse Management and Infor WMS. To delve deeper into integration possibilities with Makini and Six Sigma in manufacturing, it is advisable to contact Makini directly for detailed information.
3. Case Study: Improving Inventory Optimization using Six Sigma and Makini Platform
In the manufacturing sector, the Six Sigma methodology when combined with advanced solutions can effectively address operational inefficiencies, especially in the area of inventory management. Take, for instance, Southern Wine Spirits, the largest wine and spirits distributor in the U.S. They faced issues with operational expansion, order accuracy, system efficiency, and inventory visibility. To resolve these obstacles, they engaged Bastian Solutions, a world-renowned material handling system integrator. The company utilized Bastian's ExactaWCS warehouse control system, automated order routing, and voice-directed picking devices, among other technologies.
The incorporation of these technological solutions led to a significant upgrade in their operational efficiency. A striking 62% increase in daily shipped orders was observed, enhancing customer service due to improved system efficiency and order accuracy. Additionally, the company gained a complete overview of orders across the system, optimizing their inventory management.
Another example of how a blend of Six Sigma methodology and innovative solutions can make a considerable difference is Nine Line Apparel. Aiming to augment storage capacity and organization in their production and fulfillment facility, the lifestyle brand based in Savannah, GA collaborated with Bastian Solutions. A suite of technologies, including selective rack for static storage, pushback rack for dynamic storage, and carton flow racking, was implemented.
The outcome was a total transformation of their storage system, enabling the storage of up to 1,100 pallets and 6,000 SKUs. Before this, due to insufficient storage space, the company had to store products outside. However, with the new infrastructure, Nine Line Apparel could efficiently store all products within the facility, improving inventory management and reducing customer lead times.
In these case studies, we see how the Six Sigma methodology, coupled with innovative solutions and technologies, can substantially improve operational efficiency, particularly in inventory management. Identifying and addressing the root causes of inefficiencies allows companies to optimize operational performance, reduce costs, and improve customer service.
Now, let's look at a modern solution like Makini, an inventory management platform. With Makini's inventory optimization feature, businesses can analyze and manage their inventory more effectively. By identifying trends, forecasting demand, and making data-driven decisions, Makini helps reduce stockouts, minimize carrying costs, and improve overall supply chain efficiency. This platform offers various solutions for inventory management, helping businesses improve their cash flow through effective inventory management strategies. With Makini, companies can ensure that the right amount of inventory is available at the right time, ultimately leading to improved cash flow. The platform also supports real-time inventory management, providing businesses with up-to-date visibility and control over their inventory.
As demonstrated, the combination of methodologies like Six Sigma and modern solutions like Makini can significantly enhance operational efficiency, particularly in inventory management. This blend allows businesses to approach their operational challenges strategically, leading to optimized performance and reduced costs.
4. Case Study: Streamlining Maintenance Processes through Six Sigma and Makini API Integration
A paradigm shift was brought about in a regional American airline's operations, courtesy of the adoption of the Veryon Defect Analysis tool. The airline, with a diverse fleet of over 130 aircraft including models like Boeing 737, Q400 Dash 8, Embraer 175, and CRJ 900, grappled with the identification and documentation of recurring faults. The challenge was magnified by the cumbersome task of analysing the historical data of their aircraft, which was a significant barrier to visibility and the accurate identification of root causes.
The introduction of Veryon Defect Analysis, an innovative tool harnessing the power of natural language processing and machine learning to delve into defect texts, marked a turning point. The software was instrumental in mitigating human error in defect reporting and enhancing the precision of defect searches. The outcome was impressive - a 20% cut in repeat discrepancies and a tenfold reduction in time spent on researching the entire fleet. This represented a significant time-saving measure for the airline, and it also contributed to the improvement of their fleet's overall health.
The benefits of adopting the Veryon Defect Analysis tool did not end with time-saving. It also facilitated an overall projected savings of $400k in costs across the company. The cost savings were attributed to the tool's effectiveness in reducing delays and cancellations, enhancing safety, ensuring efficient utilization of parts, and improving parts availability.
In a parallel development, Trumpf, a pioneer in industrial laser technology, collaborated with Eoda, a data science firm, to introduce predictive maintenance through data analysis. This was accomplished by empowering Trumpf's data science team to analyse machine data using the R programming language. The outcome was a condition monitoring portal based on the Yuna solution. This portal facilitated Trumpf to keep tabs on machine condition and optimize maintenance efforts and costs. It served as a bridge between disparate departments, fostering collaborative work on data science use cases.
The successful introduction of predictive maintenance led to a decrease in downtime, a rise in machine availability, and optimization of service processes. Trumpf was able to preemptively detect machine malfunctions, culminating in an increase in the availability of its machines. Furthermore, the successful integration of this predictive maintenance approach has spurred other digital initiatives within the company, laying the groundwork for data-driven business models by integrating data science into their existing business processes.
Similarly, Makini.io offers a suite of solutions that cater to maintenance and productivity. By providing real-time maintenance data, it enables users to boost productivity by offering insights into the performance and status of their equipment and assets. This data facilitates proactive maintenance planning and scheduling, which reduces downtime and optimizes resource allocation. Businesses leveraging Makini's real-time maintenance data can significantly enhance their operational efficiency and productivity.
5. Real-world Project: Overcoming Operational Challenges with Six Sigma and Makini Link Feature
In the demanding world of manufacturing, the key to thriving lies in operational efficiency. This was the realization for a manufacturing enterprise that found itself hindered by operational roadblocks, primarily due to the absence of departmental synchronization. This issue wasn't exclusive to this enterprise, but a widespread challenge across the industry. To overcome this, the company took bold steps by incorporating the Six Sigma methodology into their operational practices.
Six Sigma, a data-driven approach, aids in identifying and eradicating inefficiencies in processes. When the company implemented it, it resulted in a thorough scrutiny of their existing procedures, thereby spotlighting areas of inefficiency that had previously gone unnoticed. It was like shedding light on the hidden aspects of their operational practices, highlighting areas that needed rectification.
Upon identifying the issues, the company didn't just stop there. They leveraged the Link feature offered by Makini, a tool designed for data integration across various departments. This feature acted as a conduit, connecting the isolated data islands that were scattered across different departments. The amalgamation of data facilitated enhanced collaboration and decision-making across departments, thereby tearing down the barriers that previously impeded coordination.
This integration process was made seamless by Makini's Link feature, eliminating the need for manual data transfer and reducing the risk of errors or inconsistencies. It also enabled real-time updates of integrated data, reflecting any changes made to the source data immediately. This ensured that the users had access to the most current information, enhancing efficiency and data management. Moreover, it provided a comprehensive view of their data, promoting deeper insights and analysis.
Their journey towards operational efficiency was further bolstered by integrating Makini's software solutions with various warehouse management systems such as Oracle Fusion Cloud Warehouse Management and Manhattan Associates Warehouse Management IBM. This integration streamlined their operations, improved productivity, reduced waste, and aligned with the principles of Six Sigma.
The outcome of these alterations was transformative. The company noticed a substantial enhancement in their operational efficiency and effectiveness. The camaraderie among departments improved, and decisions were made more efficiently, thanks to the integrated data provided by Makini's Link feature. This case is a testament to the transformative power of Six Sigma and the potential of tools like Makini's Link feature in augmenting operational efficiency in the manufacturing industry.
6. Case Study: Achieving Operational Excellence using Six Sigma Methodology and Makini's Rapid Integration Capabilities
In their quest for operational excellence, a manufacturing firm incorporated the Six Sigma methodology to refine its procedures. The main challenge faced was handling and synchronizing data across various platforms. This changed with the introduction of Makini's swift integration capabilities, which served as a game-changer for the firm. Makini functioned as a unified data source, simplifying data access and management.
The unified system facilitated the firm to measure, analyze, and improve their processes effectively. The outcome was a notable enhancement in operational performance, propelling the firm towards the zenith of operational excellence. The efficient processes and effective data management brought about by Makini's rapid integration system played a key role in this transformation.
Integrating Six Sigma and data management with Makini was a careful process, adhering to best practices. Clear objectives were defined for the Six Sigma and data management initiatives, identifying specific areas where Makini could improve efficiency, reduce errors, and enhance data analysis. Data standardization was a priority, ensuring consistency across all systems and processes. Data governance practices were implemented to maintain data quality and integrity.
Process mapping was utilized to identify areas of improvement and potential bottlenecks. Makini's integration capabilities helped streamline data flow and automate processes wherever possible. The firm leveraged Makini's data analytics tools for data analysis and reporting, identifying trends, and making informed decisions. Standardized reports and dashboards were developed to monitor performance and track progress regularly.
A culture of continuous improvement was instilled within the organization. Employees were encouraged to identify areas for improvement and provide feedback on how Makini could be used more effectively. Adequate training and support were provided to employees on using Makini effectively for data management and Six Sigma initiatives, ensuring everyone was familiar with the tools and processes and could maximize their potential.
Makini's capabilities were further utilized by integrating with various warehouse management systems, such as Oracle Fusion Cloud and Infor WMS. This helped streamline processes and data management in the context of warehouse operations, enhancing their Six Sigma processes and improving data management efficiency.
The integration of Six Sigma and data management with Makini was a thoughtful process, considering several key points. Makini's integrations with various warehouse management systems, such as Oracle Fusion Cloud and Manhattan Associates, were evaluated to align with the principles and methodologies of Six Sigma. This involved assessing data quality, process standardization, and performance measurement capabilities within Makini's integrations. Clear communication channels and collaboration frameworks were established between the Six Sigma team and the data management team, ensuring successful integration and implementation of Six Sigma principles within Makini's platform.
7. The Impact of Implementing Six Sigma on Strategic Goals and Objectives in Manufacturing
The adoption of Six Sigma methodologies within the manufacturing landscape is a critical catalyst for the realization of strategic goals and objectives. By striving for near-perfect quality, manufacturers can reduce costs, elevate customer satisfaction, and enhance operational efficiency. The integration of industrial systems via platforms such as Makini allows for real-time data access, facilitating informed decision-making and performance measurement against strategic targets. This enables the timely implementation of improvements, driving the organization towards its strategic objectives.
A case in point is the food processing equipment manufacturer, Marel. Through the implementation of Lean Six Sigma, Marel was able to significantly reduce the number of warranty claims, saving $240,000 annually. The Lean Six Sigma project saw the team perform a process gemba walk, identifying wastage and communication gaps. By implementing targeted solutions, including role clarification, standard work procedure creation, and training, Marel improved its warranty claims process, realizing substantial cost savings.
In another instance, Kyocera AVX, a global electronic components manufacturer, sought to maintain quality management systems and continuous improvement programs across its international manufacturing facilities. To achieve this, the company implemented Minitab Engage, a software solution that facilitated global information sharing and collaboration. Minitab Engage provided standardized templates for the 8 Discipline (8D) problem-solving process, helping manage customer complaints and meet ISO requirements. The software also automated certain functions and created dashboards for summary metrics. As a result, Kyocera AVX realized improved teamwork, collaboration, and information sharing, leading to cost avoidance and a faster response to customer needs.
These examples highlight the transformative potential of Six Sigma and effective industrial integration. When leveraged correctly, they can drive manufacturing companies towards achieving their strategic objectives, improving product quality, reducing costs, increasing customer satisfaction, and enhancing operational efficiency.
Conclusion
In conclusion, the implementation of Six Sigma methodologies in manufacturing has a significant impact on strategic goals and objectives. By utilizing statistical tools and techniques, businesses can identify process inefficiencies, reduce waste, improve cycle times, and enhance product quality. Real-world case studies have demonstrated the effectiveness of Six Sigma in improving operational efficiency, reducing costs, and increasing customer satisfaction. The integration of industrial systems through platforms like Makini plays a crucial role in enabling seamless data synchronization and promoting collaboration across departments. By understanding the benefits of Six Sigma and effective industrial integration, businesses can achieve their strategic objectives and drive success in the manufacturing industry.
The broader significance of implementing Six Sigma and industrial integration lies in the pursuit of operational excellence and improved customer satisfaction. By streamlining processes, reducing defects, and optimizing performance, businesses can achieve maximum efficiency in their operations. The use of statistical tools and techniques allows for data-driven decision-making, leading to informed improvements that enhance product quality and reduce costs. Industrial integration platforms like Makini enable real-time monitoring, facilitate collaboration across departments, and simplify data transmission. By embracing Six Sigma methodologies and leveraging industrial integration platforms like Makini, businesses can drive operational excellence, meet strategic goals, and thrive in the competitive manufacturing industry.