Introduction
The manufacturing industry is constantly striving for operational excellence to optimize efficiency, reduce costs, and enhance productivity. One key aspect of achieving operational excellence is through industrial integration, which involves seamlessly connecting various systems and processes within an organization. Industrial integration enables real-time data retrieval, streamlines operations, and enhances decision-making capabilities. By leveraging technologies such as IoT, AI, and machine learning, manufacturers can transform their operations and drive operational excellence.
In this article, we will explore the impact of industrial integration on manufacturing processes and the benefits it brings to inventory optimization and aftermarket processes. We will also delve into the future of manufacturing with Industry 4.0 and how it influences operational excellence. By understanding the role of industrial integration in achieving efficiency and exploring emerging trends in the manufacturing industry, organizations can position themselves for success and stay ahead in an increasingly competitive landscape.
1. Understanding the Concept of Operational Excellence in Manufacturing
The journey to operational excellence in the manufacturing industry is a continuous endeavor. It requires an integrative approach, encompassing all aspects of the organization, from fostering a conducive environment that promotes problem-solving and leadership, to creating a workspace that values safety, quality, cost-efficiency, and employee morale.
A critical tool in this journey is the Overall Equipment Effectiveness (OEE) metric, a gold standard in measuring manufacturing productivity. OEE quantifies the percentage of truly productive manufacturing time. An ideal OEE score of 100% signifies that manufacturing is producing only good parts, as fast as possible, with zero stop time.
Availability, performance, and quality are the key components of the OEE metric. Availability measures the ability of the process to run during planned production time, accounting for both unplanned and planned stops. Performance gauges how fast the process runs when it is running, considering slow cycles and minor stops. Quality, on the other hand, quantifies the number of defects or parts that require rework.
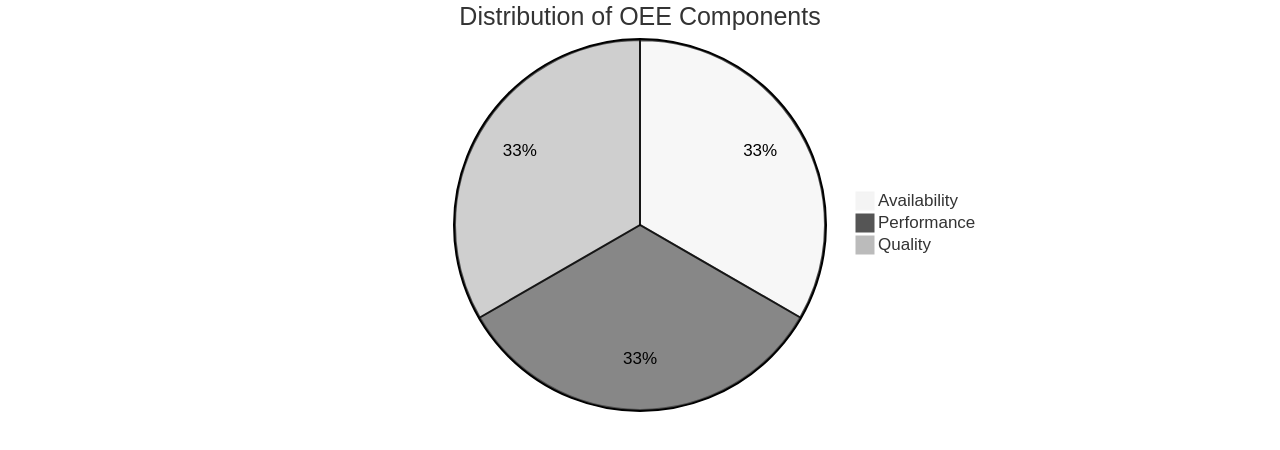
Six major losses can impact OEE, namely equipment breakdowns, setup and adjustment time, idling and minor stoppages, reduced speed, defects and rework, and startup and yield losses. Identifying and addressing these losses forms the foundation of Total Productive Maintenance (TPM), which can lead to significant improvements in OEE.
To effectively navigate this journey, manufacturers can leverage tools like the Vorne XL. This fully integrated IoT device monitors production and provides real-time alerts, enabling operators to respond promptly to any issues that may arise. It also offers a powerful reporting suite for managers and supervisors, providing them with the insights needed to make informed decisions.
Vorne Industries, the company behind Vorne XL, specializes in improving manufacturing productivity. They offer a range of free tools, tips, and resources to help manufacturers learn about and improve OEE. These resources include leadership lessons, training guides, and project organizers, which can be accessed by signing up for their monthly newsletter.
However, achieving operational excellence goes beyond implementing effective metrics and leveraging advanced tools. It requires the adoption of best practices that optimize processes, increase efficiency, and ensure quality. These practices include Lean Manufacturing, Total Quality Management (TQM), Six Sigma, Supply Chain Optimization, Automation and Technology, and Employee Empowerment.
To align all aspects of an organization for operational excellence, it is crucial to establish clear goals and objectives that align with the organization's overall vision and mission. Fostering a culture of continuous improvement, encouraging effective communication and collaboration across all levels of the organization, and providing necessary resources, tools, and training to employees are all strategies that can contribute to achieving operational excellence.
Moreover, improving problem-solving techniques for continuous improvement in manufacturing entails implementing a structured approach such as the PDCA (Plan-Do-Check-Act) cycle. Using tools such as cause-and-effect diagrams, Pareto charts, and process flowcharts can aid in identifying and understanding underlying issues.
To ensure safety and quality for operational excellence in manufacturing, it is essential to implement robust processes and systems. This includes conducting regular inspections to identify any potential hazards or defects in the manufacturing process and providing comprehensive training to all employees to ensure they are aware of safety protocols and quality standards.
Lastly, optimizing costs and ensuring on-time delivery of products are crucial aspects of operational excellence in manufacturing. This can be achieved through efficient inventory management, implementing lean manufacturing principles, leveraging advanced analytics and data-driven decision-making, and having efficient warehouse management systems in place.
In essence, operational excellence in manufacturing is a holistic endeavor that engages everyone in the organization. It's a journey that requires continuous improvement, leveraging best practices, and tools to measure and enhance productivity, ultimately leading to a more efficient, effective, and profitable manufacturing process.
2. The Role of Industrial Integration in Achieving Operational Excellence
Industrial integration serves as a vital component of operational excellence within the manufacturing sector. By bridging the gap between various industrial systems, such as maintenance and asset management systems, it enables the swift retrieval of data. This immediate access to information empowers organizations to make well-informed, timely decisions.
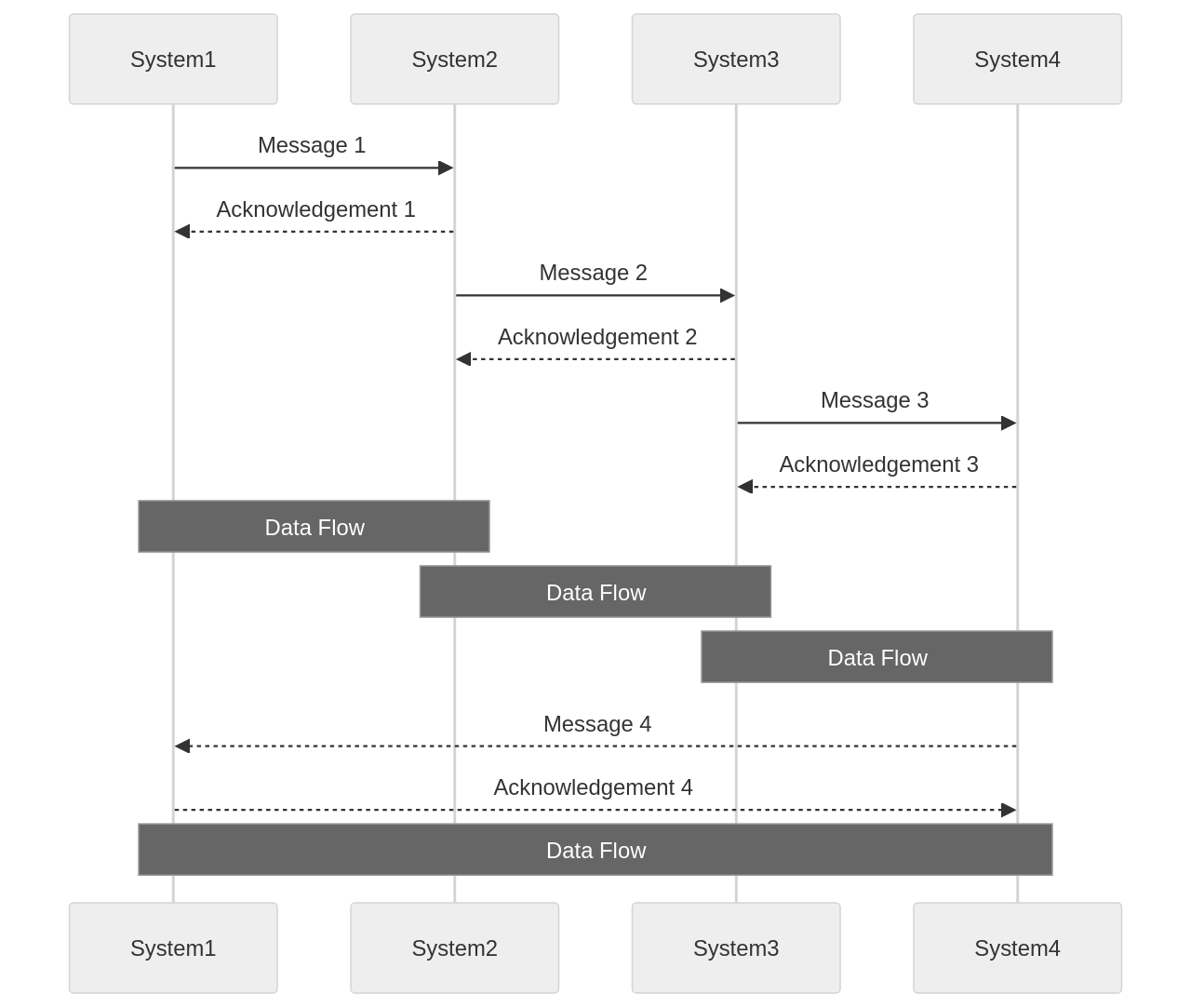
The amalgamation of multiple industrial systems not only bolsters decision-making capabilities, but also eliminates the need to juggle disparate data structures, authorization protocols, and data transformations. This eradicates unnecessary complexities, thereby streamlining operations, optimizing efficiency, and reducing recurrent issues that can lead to financial losses. It's a well-established fact in operations that mitigating the potential for negative events always provides a sense of assurance. Yet, numerous minor, recurrent issues can escalate into considerable problems if not properly managed, frequently resulting in significant production and financial losses.
Manufacturing operations often present a labyrinth of complexities, posing a significant challenge for executives. Industrial integration serves as an instrumental tool in their toolkit to counteract this complexity. It enables organizations to fine-tune their operations, optimize processes for improved efficiency, and reduce the length of the supply chain. Furthermore, executives are progressively prioritizing the need to address the complexities challenge, with nearly 90% of them rating it as a significant concern.
In addition, the role of ERP systems within manufacturing companies is evolving beyond merely monitoring and automating business performance functions. These systems are now perceived as the backbone of manufacturing enterprises, fostering collaboration and communication, accelerating decision-making, and offering advanced analytics capabilities. However, it's worth noting that many companies fail to harness the full business benefits of ERP software in manufacturing. This underlines the necessity for achieving harmony among diverse ERP systems.
Industrial integration is a powerful tool at the disposal of manufacturing companies to enhance their operational efficiency. It not only streamlines operations and optimizes efficiency but also equips organizations with the capability to make well-informed, timely decisions. Therefore, it's crucial for manufacturing companies to consistently invest in and amplify their industrial integration capabilities to maintain a competitive edge in the increasingly complex world of manufacturing.
Industrial integration can be significantly bolstered by integrating various systems and processes within an industrial setting, thereby streamlining operations, improving efficiency, and enhancing overall productivity. By ensuring seamless communication and data exchange between various departments, suppliers, and partners, organizations can achieve better coordination and collaboration. This, in turn, allows organizations to optimize resource allocation, reduce redundancies, and eliminate bottlenecks, ultimately driving operational excellence.
Enhance operational excellence with industrial integration!
Industrial integration also facilitates real-time monitoring and analysis of data, enabling organizations to make informed decisions, identify areas for improvement, and implement corrective actions promptly. Moreover, real-time data retrieval in industrial integration provides numerous benefits, including immediate access to up-to-date information, enabling faster decision-making and response times, and providing accurate and reliable data, reducing the risk of errors, and improving overall data quality.
Integration solutions specifically designed for industrial settings enable the exchange of data and communication between different industrial systems, allowing for real-time monitoring and improved coordination. Warehouse management systems such as Oracle Fusion Cloud Warehouse Management and Manhattan Associates Warehouse Management IBM can be integrated with maintenance and asset management systems, optimizing workflows and improving overall operational efficiency.
Lastly, dealing with multiple data structures in industrial integration can be challenging. However, solutions are available that can help manage these challenges. By implementing authorization protocols, organizations can control access to their systems and ensure that sensitive data and operations are protected. Data transformations can also play a crucial role in industrial integration by ensuring interoperability and compatibility between different systems and platforms.
Overall, industrial integration is a crucial aspect for organizations seeking to achieve operational excellence by maximizing their operational efficiency and effectiveness.
3. Overcoming Challenges to Operational Excellence: Lack of Coordination and Streamlining Processes
As manufacturing entities strive for operational excellence, obstacles often emerge in the form of disjointed departments and unprocessed workflows. These hurdles, if overlooked, can decimate efficiency and disrupt seamless operations. However, the dawn of industrial integration ushers in a new epoch of heightened inter-departmental coordination and communication, thereby enhancing operational efficacy.
For example, China Manufacturing Consultants (CMC) achieved a significant cost reduction in a Chinese factory without the use of automation. This accomplishment was made possible through the vigorous engagement of workers, a critical component in the success of the transformation. CMC collaborated with top management to establish lean-style manufacturing lines, resulting in increased productivity and pace. This involved the rearrangement of assembly lines and the implementation of a comprehensive 6-month training program that covered a broad spectrum of subjects, from lean training to preventive maintenance and material control.
The impact of these initiatives was monumental. The factory's cost structure was reduced by 15 million USD per year, and the reengineering of the assembly line not only improved quality but also led to a reduction in production operators. Furthermore, administrative support processes were streamlined, leading to a reduction in indirect workers. Better inventory control resulted in significant savings, and the increased capacity enabled the factory to accept new business, which subsequently led to an additional 15 million USD in profit per year.
Another remarkable case is Kyocera Corporation, a company that aims to double its manufacturing productivity. To reach this ambitious goal, the company initiated unmanned production lines powered by AI and robots to enhance manufacturing efficiency. The key principle here is "autonomous" production, where AI is utilized to analyze real-time data and make adjustments to prevent defective products and machine breakdowns.
Kyocera's collaboration with IBM played a crucial role in promoting the productivity doubling project. IBM provided solutions for building a digital platform that integrated production planning, scheduling, and production management systems to enable uninterrupted autonomous production lines. The platform also collected and analyzed data from production sites in real-time to predict and prevent defective products. The system's insights were then used to change workflows and free operators to concentrate on higher-value work. This approach has already shown quality improvement results, including a nearly 6% increase in yield rate in the production of fine ceramics, improved price competitiveness, increased capacity utilization rates, and reduced costs.
These examples underscore the transformative power of industrial integration in overcoming operational challenges and achieving operational excellence. By fostering better coordination and communication between departments, this approach can significantly enhance operational efficiency, leading to cost savings and improved productivity.
To enhance this coordination, one could implement a centralized system that allows departments to share information and updates in real-time. This could include using project management software, setting up regular meetings and check-ins, and encouraging cross-departmental collaboration and knowledge sharing. Additionally, establishing clear roles and responsibilities for each department and ensuring that there is a clear understanding of how each department's work contributes to the overall goals of the organization can also improve coordination. Regular communication, feedback, and performance evaluations can help identify and address any gaps or issues in coordination between departments.
Streamlining processes across multiple departments with industrial integration can offer several benefits. By integrating different departments within an organization, companies can improve communication and collaboration, leading to increased efficiency and productivity. This integration can also help eliminate redundant or duplicate tasks, reducing costs and saving time. Additionally, streamlining processes can provide better visibility and tracking of data throughout the organization, enabling better decision-making and strategic planning.
To achieve operational excellence through industrial integration, it is important to follow best practices that can optimize processes and enhance overall efficiency. This can include implementing a robust integration strategy, leveraging advanced technologies, and fostering collaboration between different systems and stakeholders. By integrating various industrial systems and processes, organizations can streamline operations, improve data accuracy, and enable real-time visibility into their supply chain and warehouse management. This can lead to improved decision-making, reduced costs, enhanced customer satisfaction, and ultimately, operational excellence.
Achieve operational excellence with industrial integration!
In conclusion, the key to overcoming operational challenges and achieving operational excellence lies in the successful implementation of industrial integration. By fostering better coordination and communication between departments, streamlining processes, and following best practices, organizations can significantly enhance operational efficiency, leading to cost savings and improved productivity.
4. How Real-Time Data Retrieval Contributes to Operational Efficiency
The advent of real-time data retrieval has revolutionized operational efficiency, providing businesses with the tools to make swift, informed decisions, substantially reducing downtime, and enhancing productivity. This is particularly evident in the realm of industrial integration, where the immediate and secure access to data propels operational efficiency to new heights.
Asia's largest retail conglomerate, Central Group, is a testament to this transformation. The backbone of their real-time analytics is QuestDB, a system that handles data from a plethora of sources, both online and offline, across their diverse business sectors. This data is transformed into actionable dashboards, individually tailored for specific teams across each business unit.
This real-time data is showcased on large screens throughout their offices, enabling rapid monitoring and response to any unusual data patterns. This setup is akin to a business control tower, providing real-time statistics fueling their business modeling and data-driven marketing strategies.
One such application is Central Group's marketing performance tracking dashboard, powered by QuestDB. This system enables dynamic comparisons between various advertisement platforms and has the capability to correlate online sales with the geographical presence of their department stores. This integration offers a comprehensive view of the business operations, aiding decision-making, and ultimately enhancing operational efficiency.
Central Group's real-time data retrieval system employs a dedicated change data capture process to collect data from various sources. This data is then streamed into QuestDB in real-time. Approximately ten Grafana dashboards constantly query QuestDB for real-time analytics and time series charts. QuestDB was chosen for its superior performance, ease of integration with Grafana, and lower hardware costs compared to alternatives like InfluxDB and SingleStore.
Another example of operational efficiency through real-time data retrieval is tech giant Microsoft. Their diverse product and service offerings, from Microsoft Security to Azure, Dynamics 365, Microsoft 365, and Microsoft Teams, signify their commitment to tech innovation. Advancements in cloud computing, artificial intelligence, mixed reality, and quantum computing serve diverse industries, including education, automotive, financial services, government, healthcare, and manufacturing, enhancing efficiency across various sectors.
These examples underline the transformative power of real-time data retrieval in achieving operational efficiency. Industrial integration enables swift and secure access to data, allowing informed decisions that enhance productivity. Whether it's a retail sector leveraging real-time analytics to optimize operations or a tech company innovating to serve diverse industries, the potential of real-time data retrieval is boundless.
Real-time data retrieval is a critical component of industrial integration, ensuring immediate access to the most current data. It is particularly beneficial in industries where decisions need to be made based on the most current data. By retrieving data in real-time, companies can optimize their operations, improve efficiency, and make informed decisions.
Real-time data retrieval also allows better monitoring of processes, detecting issues or anomalies as they occur, and taking immediate corrective actions.
When implementing real-time data retrieval in industrial integration, it's important to have a reliable and secure connection to the data source. This can involve using secure protocols such as HTTPS and implementing authentication mechanisms to protect the data. It's also crucial to design the integration system to minimize latency, by optimizing the data retrieval process, such as using efficient algorithms and caching mechanisms.
Monitoring and error handling are also crucial aspects of implementing real-time data retrieval. It's important to have monitoring mechanisms in place to track the performance and availability of the integration system. Additionally, proper error handling should be implemented to handle any failures or exceptions that may occur during the data retrieval process.
There are various tools and technologies available for real-time data retrieval in industrial integration. Some commonly used tools include APIs (Application Programming Interfaces), MQTT (Message Queuing Telemetry Transport), OPC (OLE for Process Control), Data Integration Platforms, and Cloud-based Services.
In conclusion, real-time data retrieval empowers organizations across various industries to make data-driven decisions, enhance operational efficiency, and achieve higher productivity levels. Whether in the manufacturing sector, logistics and supply chain industry, or the retail sector, real-time data retrieval allows for optimization of various processes, ultimately driving increased productivity.
5. The Impact of Rapid Industrial Integrations on Manufacturing Processes
The transformational wave of digital technology has revolutionized the manufacturing sector, with the integration of IoT and IIoT (Industrial IoT) systems gaining momentum. This seamless interaction has simplified operational processes, led to considerable efficiency improvements and cost reductions.
The essence of this transformation lies in the extensive grid of sensors and devices connected via IoT, an integral part of the manufacturing industry. The data generated by these devices, when collected, stored, and analyzed in real or near-real-time, provides valuable insights for decision-making.
One platform that facilitates this transformation is MongoDB's data platform. It enables manufacturers to store and analyze large volumes of data generated by IoT devices, providing real-time insights and control, thus enhancing efficiency and productivity of the manufacturing process.
The versatility of MongoDB allows integration with other technologies and platforms, streamlining data flows and processes in manufacturing. This has been showcased by a small-scale smart fabrication factory model using fischertechnik, demonstrating how IIoT use cases can be built on MongoDB's data platform.
The use of MongoDB Atlas and Realm in this model offers scalability and flexibility, and enables real-time analytics for IIoT applications. Furthermore, MongoDB natively supports time series data, facilitating a quick analysis of trends and anomalies.
The partnership between MongoDB Atlas and Google Cloud, along with HCL Technologies, provides a centralized, scalable, and cost-effective solution for data storage and analytics across various industries. This amalgamation presents an integrated suite of services for storage, analysis, and visualization, supporting data pipelines and interactive dashboards.
However, the swift digital integration in the manufacturing sector necessitates heightened security measures. MongoDB has taken steps to provide customers with indicators of compromise (IOCs) so they can proactively monitor and implement necessary security measures. Customers are also encouraged to be vigilant against social engineering and phishing attacks and to enable phishing-resistant multifactor authentication (MFA).
To streamline manufacturing processes with rapid industrial integrations, one approach is to leverage the integrations offered by Makini.io. This platform provides integrations with various warehouse management systems, such as Oracle Fusion Cloud Warehouse Management and SAP Extended Warehouse Management, automating and optimizing various aspects of operations, including inventory management, order fulfillment, and supply chain visibility. These integrations enable real-time data exchange and seamless coordination between manufacturing processes and warehouse management systems, resulting in improved efficiency and productivity.
Optimize your manufacturing processes with Makini.io integrations!
Cost savings through rapid industrial integrations can be achieved by leveraging the integrations provided by Makini.io. Their platform offers seamless integration with popular warehouse management systems such as Oracle Fusion Cloud and Manhattan Associates, optimizing supply chain processes, reducing manual effort, and minimizing errors, leading to cost savings through improved operational efficiency and increased productivity.
To achieve operational excellence with rapid industrial integrations, it is important to have a robust and efficient integration system in place. Integrating various industrial systems and processes seamlessly can streamline operations, improve productivity, and drive overall efficiency.
Achieving efficient industrial integrations requires following certain best practices. These include defining clear objectives, planning ahead, using standardized protocols, ensuring data quality, testing thoroughly, and implementing effective monitoring and maintenance processes. By adhering to these practices, organizations can effectively implement rapid industrial integrations and achieve their desired outcomes.
The swift industrial integrations in the manufacturing sector have not only optimized operational efficiency but also provided a platform for organizations to focus on achieving operational excellence. This has been made possible through platforms like MongoDB's data platform and collaborations like MongoDB Atlas on Google Cloud, which offer scalable and cost-effective solutions for data storage and analytics.
6. Leveraging Industrial Integration for Inventory Optimization and Aftermarket Processes
Industrial integration elucidates its value by linking inventory management systems, enabling real-time inventory tracking. This ability not only curtails inventory expenses but also escalates customer satisfaction by ensuring the timely availability of products. A solution like Makini, which offers integrations with Oracle Fusion Cloud Warehouse Management and SAP Extended Warehouse Management, can be instrumental for industrial operators looking for real-time inventory tracking solutions. This can provide operators with precise, up-to-the-minute information about their inventory levels, enabling them to make informed decisions and optimize their operations.
A testament to the power of industrial integration is the success story of Southern Wine & Spirits of Oregon, the largest wine and spirits distributor in the U.S. They integrated a new conveyor system, pick modules, and software to enhance customer service and employee engagement. This integration resulted in a significant increase in cartons sorted per day, accuracy rates above 99.5%, decreased product breakage, and improved customer delivery times. The facility is now equipped to sort more than 1600 cartons per hour, thanks to the integration of technologies like the Exacta 60 warehouse control system, Manhattan warehouse management system, voice-directed picking devices, RF picking, and Hytrol conveyor systems.
Industrial integration isn't limited to inventory management. It also plays a key role in enhancing aftermarket processes, thereby improving the overall customer experience. Parts Town, a leading source for food service equipment parts, partnered with Bastian Solutions and implemented the Autostore goods-to-person system for high-density storage and scalability. The results were impressive, with increased order fulfillment, improved inventory space, enhanced order accuracy, and a safer, more ergonomic environment. Integrated aftermarket processes can be maximized for efficiency by streamlining operations and optimizing workflows. This can be achieved by implementing automation and digitization solutions that connect various systems and departments involved in the aftermarket processes.
In the realm of inventory optimization in industrial maintenance, several best practices can assist in improving efficiency and reducing costs. Accurate forecasting of demand, analysis of historical data, implementing an effective inventory management system, adopting a just-in-time (JIT) inventory management approach, and conducting regular inventory audits can contribute significantly to optimization. These practices, coupled with establishing strong relationships with suppliers, can lead to improved efficiency, reduced costs, and better overall performance.
In the end, industrial integration is a potent tool that can be utilized for inventory optimization and aftermarket processes, resulting in improved efficiency, lower costs, and enhanced customer satisfaction. As we continue to advance in the digital age, it's crucial for organizations to harness the power of industrial integration to drive operational excellence.
7. The Future of Manufacturing: Industry 4.0 and its Influence on Operational Excellence
The paradigm shift to Industry 4.0, the digitization of industrial processes, is changing the manufacturing landscape significantly. This change is driven by the integration of groundbreaking technologies such as the Internet of Things (IoT), artificial intelligence (AI), and machine learning. These technologies, when systematically incorporated into industrial operations, have the potential to significantly boost operational excellence.
IoT applications in manufacturing, for instance, can enhance operational efficiency and provide real-time insights. IoT devices can supervise and manage production processes, track inventory, optimize supply chain operations, and enable predictive maintenance. In addition, IoT can be used to collect and analyze data from machines and equipment, empowering manufacturers to make data-driven decisions and improve overall productivity.
Furthermore, the AI technology is increasingly being integrated across various industries, including the industrial sector. AI can be employed in industrial integration processes to boost efficiency, productivity, and decision-making. It can automate tasks, optimize workflows, and analyze large amounts of data to provide valuable insights. By leveraging AI in industrial integration, businesses can streamline their operations, cut costs, and improve overall performance.
Similarly, machine learning can be used to analyze and optimize various operational processes to achieve operational excellence. Machine learning can identify patterns and trends in data, predict outcomes, and automate decision-making processes. Applying machine learning to operational data provides organizations with insights, improves efficiency, reduces costs, and enhances overall performance.
With real-time data retrieval, manufacturers can monitor production lines, track inventory levels, and analyze performance metrics to identify inefficiencies and improve overall productivity. Real-time data retrieval allows manufacturers to react quickly to changes in demand, address quality issues promptly, and ensure that production schedules are met. This results in better resource allocation, reduced downtime, and improved customer satisfaction. By leveraging technologies such as IoT sensors, cloud computing, and data analytics, manufacturers can achieve real-time data retrieval and gain valuable insights that drive operational excellence.
Industrial integration can enhance operational efficiency by improving coordination and communication between different systems and processes. This results in streamlined workflows, reduced manual intervention, and increased accuracy in data exchange. Industrial integration can also enable real-time monitoring and analysis of operational data, leading to quicker decision-making and problem-solving. Overall, industrial integration can boost productivity, optimize resource utilization, and drive cost savings in industrial operations.
The creation of smart factories, which is largely driven by the convergence of physical and digital technologies, is a tangible reality that is progressively transforming the manufacturing sector. In these factories, machines are interconnected through IoT, enabling seamless communication and data exchange. The data generated is harnessed using AI and machine learning algorithms to derive actionable insights, inform decision-making processes, and facilitate predictive maintenance. This not only reduces downtime but also enhances the overall efficiency and productivity of the manufacturing process.
To achieve successful digital transformation in the manufacturing industry, it is important to follow some best practices. These include clearly defining digital transformation goals, building a digital culture, investing in the right technology, making data-driven decisions, collaborating with partners, and continuously improving.
In conclusion, the integration of advanced technologies into the industrial sphere, as epitomized by Industry 4.0, is revolutionizing the way manufacturing processes are carried out. It is paving the way for a more efficient, productive, and sustainable future for the manufacturing sector.
Conclusion
The integration of industrial systems and processes plays a crucial role in achieving operational excellence in the manufacturing industry. By seamlessly connecting various systems and leveraging technologies like IoT, AI, and machine learning, organizations can optimize efficiency, reduce costs, and enhance productivity. Industrial integration enables real-time data retrieval, streamlines operations, and enhances decision-making capabilities.
The impact of industrial integration on manufacturing processes is significant. It allows for real-time inventory tracking, leading to cost savings and improved customer satisfaction. It also enhances aftermarket processes by streamlining operations and optimizing workflows. Furthermore, the future of manufacturing lies in Industry 4.0, where the digitization of industrial processes through technologies like IoT, AI, and machine learning will further drive operational excellence.
To achieve operational excellence through industrial integration, organizations should invest in robust integration systems and follow best practices. This includes defining clear objectives, planning ahead, using standardized protocols, ensuring data quality, testing thoroughly, implementing effective monitoring and maintenance processes, and staying updated with the latest advancements in technology.
By understanding the role of industrial integration in achieving efficiency and embracing emerging trends in the manufacturing industry, organizations can position themselves for success and stay ahead in an increasingly competitive landscape.